L’art d’optimiser les changements de formats.
L’intervention de POMEX sur une ligne de production.
Voici comment POMEX a contribué à réduite les temps d’arrêt et augmenter la productivité lors de changements de formats.
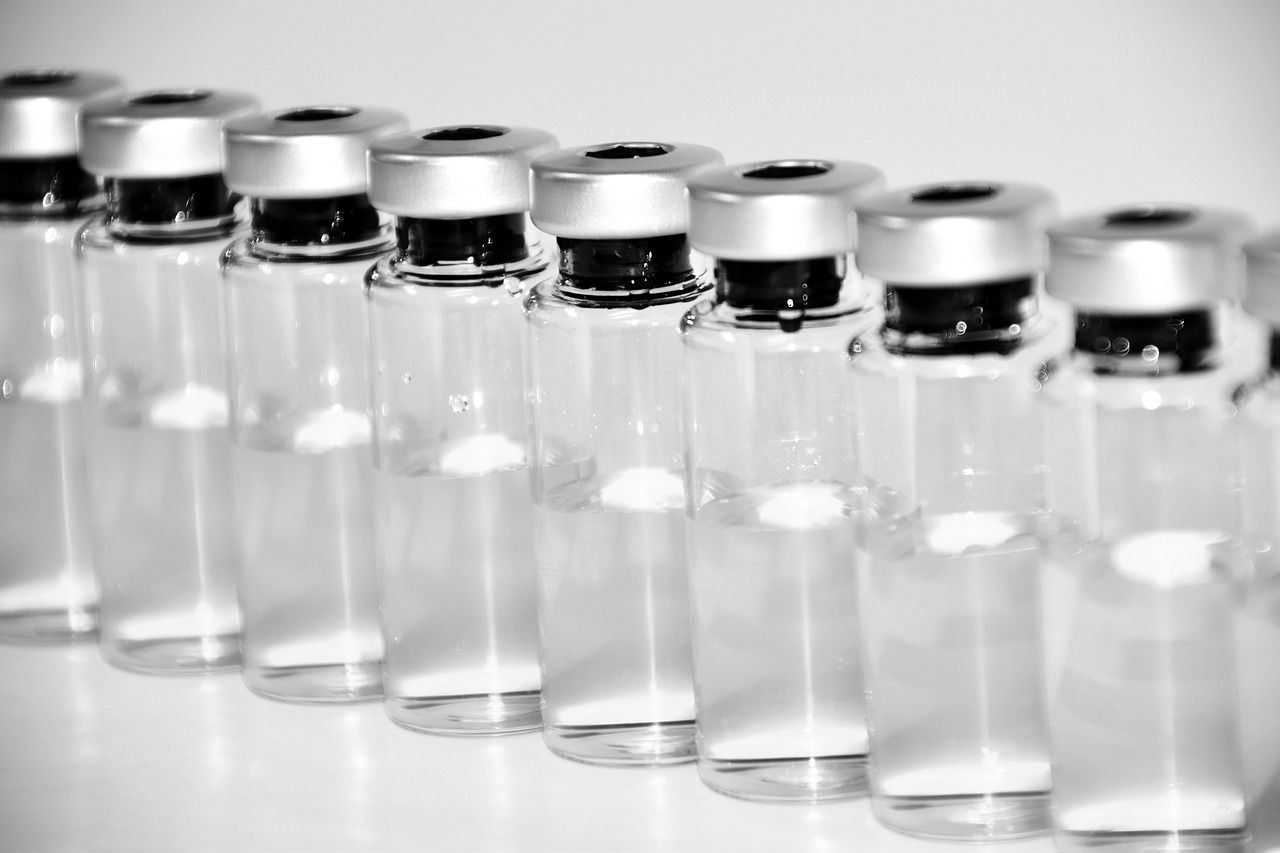
01. Contexte et problématique
L’entreprise cliente, leader dans la production à haute cadence, rencontrait des problèmes critiques liés aux changements de format sur l’une de ses lignes de production.
Ces opérations consommaient des heures, immobilisant la ligne et générant plusieurs conséquences négatives :
- Ligne inopérante : Absence de production pendant toute la durée du changement.
- Démobilisation des équipes : Une partie du personnel était sous-utilisée.
- Frustration technique : Des ajustements approximatifs au redémarrage, source de stress et d’erreurs.
Ces problèmes menaçaient directement le rendement de l’entreprise et la motivation des équipes. Le client souhaitait réduire drastiquement ces temps morts tout en évitant les problèmes de réglage au redémarrage.
02. Rôle de POMEX
Notre mission consistait à mener un projet SMED (Single Minute Exchange of Die) afin de réduire les durées de changement de format. Pour ce faire, nous avons impliqué les différentes parties prenantes : la Ligne hiérarchique, les Producteurs et techniciens, l’Équipe Opérational Excellence et le Fournisseur de l’équipement et des pièces de rechange.
En utilisant la méthode SMED, les objectifs étaient de :
- Segmenter les opérations : Identification de sous-ensembles complets à remplacer, remplaçant plusieurs heures de démontage par quelques minutes d’échange.
- Optimiser la logistique : Utilisation de chariots préparés contenant les pièces à remplacer et permettant une révision en temps masqué.
- Prévenir les erreurs : Mise en place de détrompeurs pour limiter les montages incorrects.
- Standardiser les processus : Création de procédures claires pour assurer un redémarrage éclair.
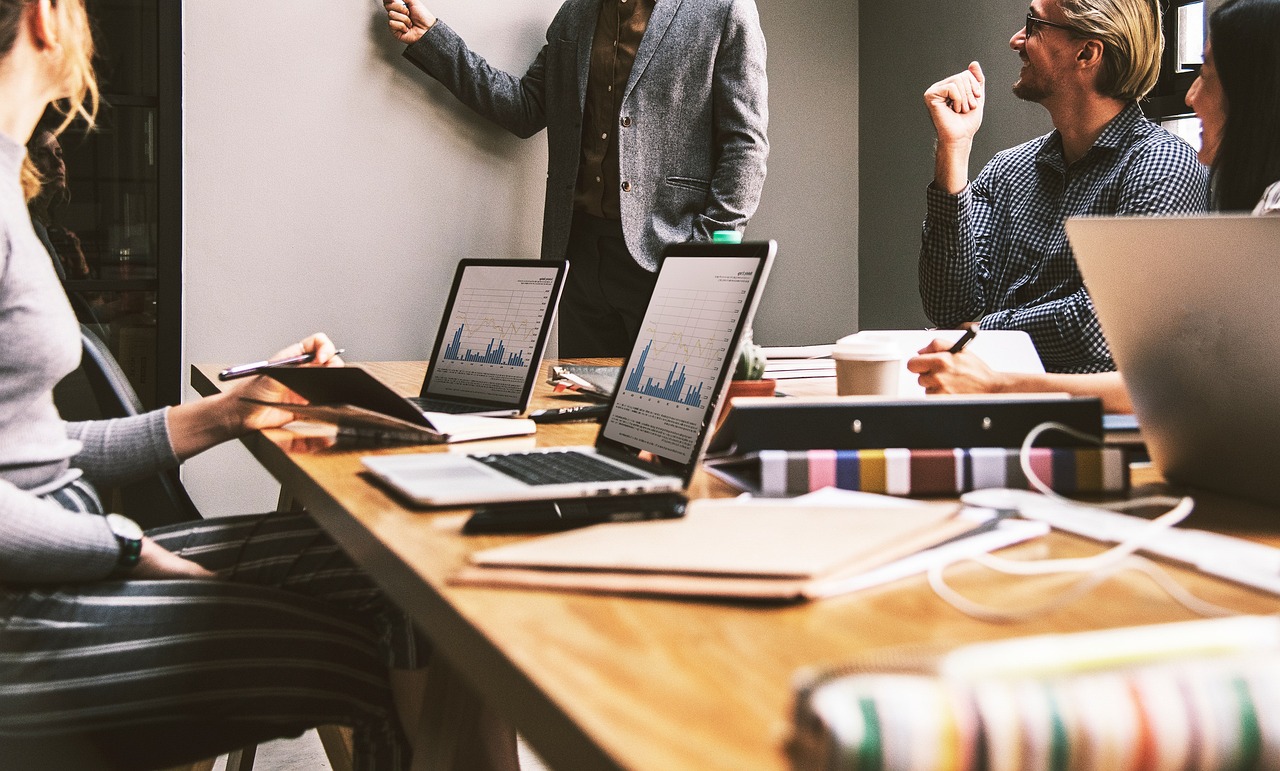
03. Solutions implémentées
Nous avons mis en place :
- La préparation des kits SMED : Pièces préassemblées et pré-réglées.
- La reconfiguration des étapes : Tests, analyse documentaire, et collaboration avec les fournisseurs pour garantir l’adéquation
- La documentation et la formation : Formalisation des procédures et sensibilisation des équipes.
04. Les résultats obtenus ?
Les solutions mises en œuvre par POMEX ont généré des résultats concrets :
- Amélioration significative du TRS : Temps de changement de format réduit de plusieurs heures à quelques minutes.
- Augmentation de la satisfaction des équipes : Suppression des ajustements approximatifs et des frustrations associées.
- Bénéfices secondaires : Fiabilisation accrue de la machine, révision systématique des composants remplacés.
Ces résultats ont été très bien reçus par les parties prenantes, renforçant la confiance et le dynamisme interne.
05. Les bénéfices à long terme
Notre client a appliqué des améliorations sur d’autres lignes de production. Cerise sur le gâteau, il a également continué à surveiller les temps de changement de format pour prévenir toute dérive.
06. L’adaptabilité
Un modèle similaire a permis de minimiser les arrêts machines pour des réparations avec des kits prêts à l’emploi. On peut également citer l’inspiration des pit stops en Formule 1 pour illustrer l’efficacité atteinte.
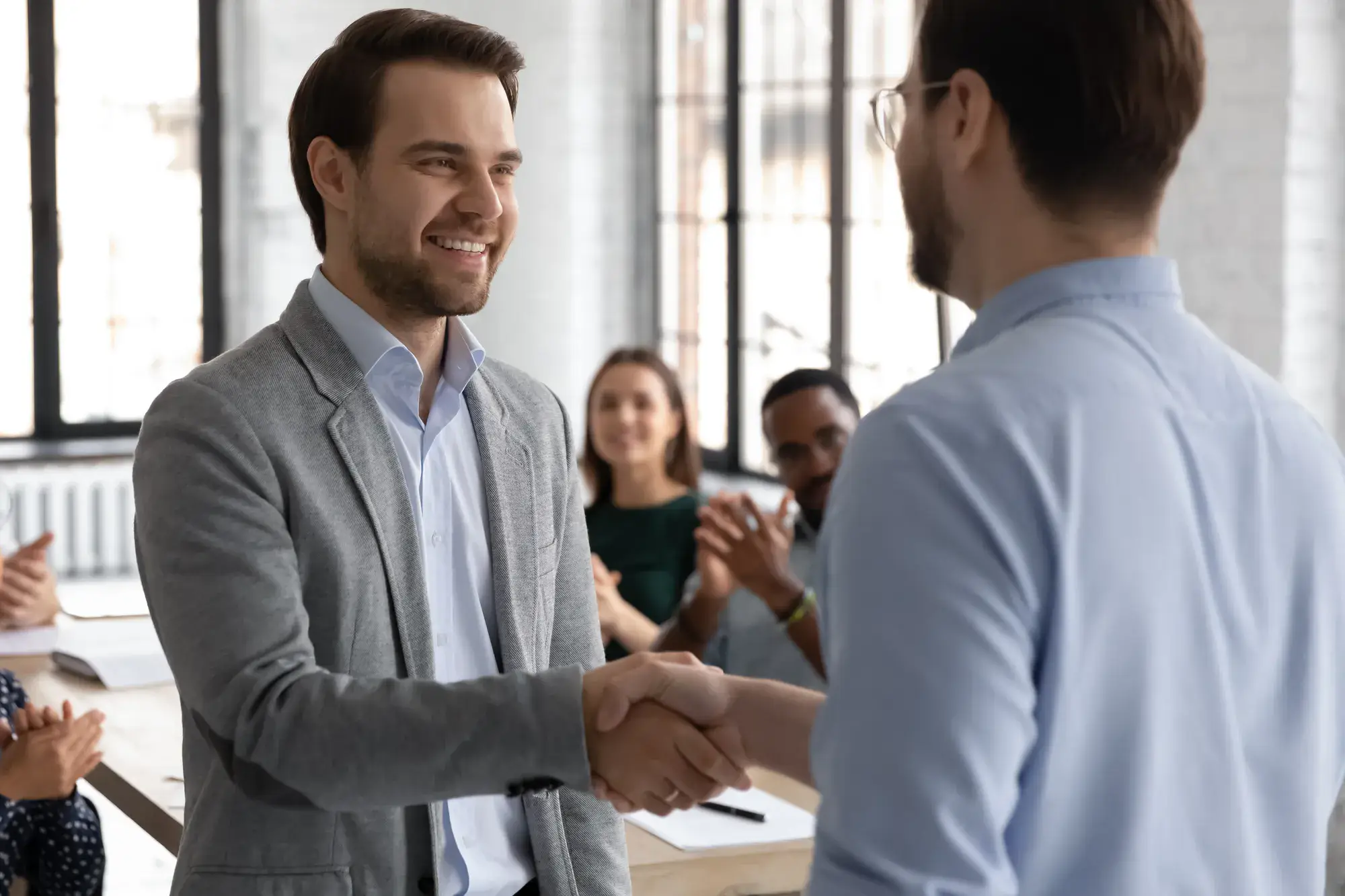
Conclusion
Ce projet a mis en évidence l’importance d’une approche structurée et collaborative pour résoudre des problèmes complexes. Il est primordial de prendre du recul, d’analyser chaque opération et de solliciter les parties prenantes.
Un dernier conseil : Filmez vos opérations pour les étudier objectivement. Impliquez toutes les équipes concernées pour garantir une solution acceptée et efficace.