How to properly manage retention systems in industrial environments for a sustainable future ?
Discover how POMEX intervened.
Retention systems in industrial environments containing tanks of hazardous solvents serve a critical role in safety and environmental protection. They must comply with a range of regulatory requirements.
POMEX helps ensure their proper maintenance.
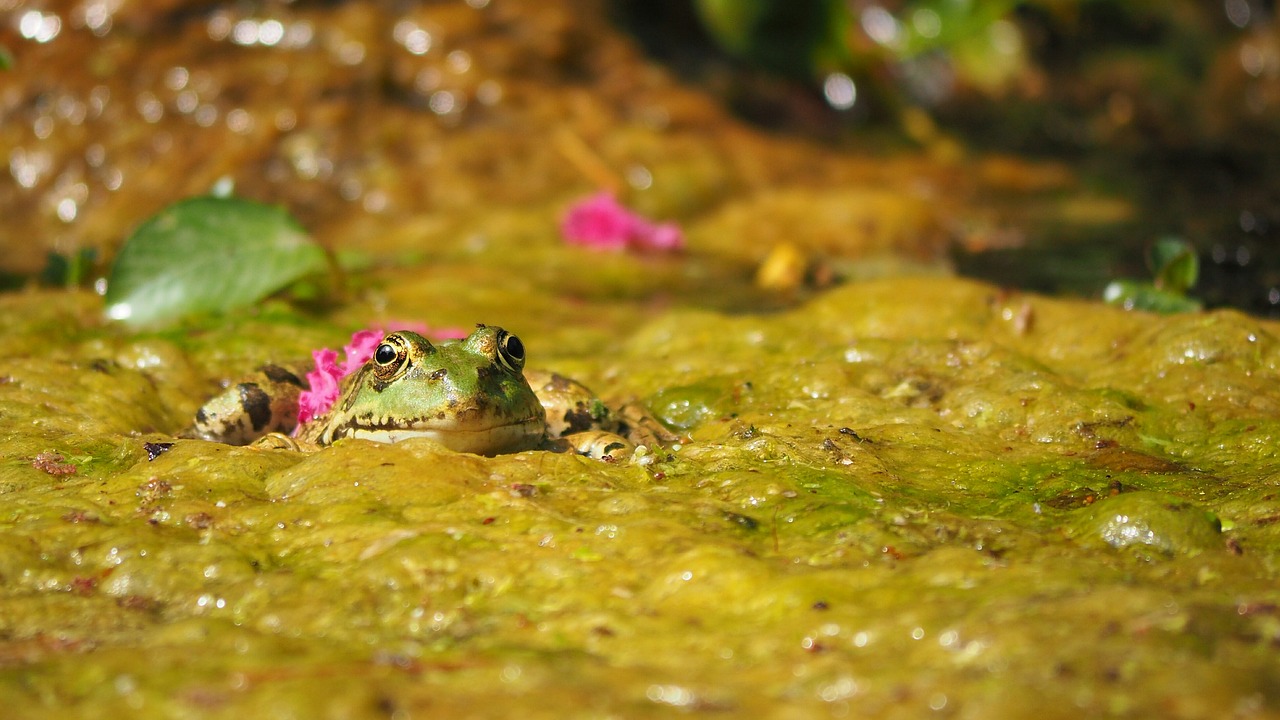
01. Context and Challenge
Retention systems in industrial settings have several essential functions :
- Preventing contamination of surrounding ecosystems by stopping hazardous chemicals or solvents from seeping into the soil, groundwater, or watercourses in the event of leaks or overflows.
- Ensuring the safety of facilities and personnel by limiting the size of areas at risk of fire or explosion associated with flammable solvents and preventing their spread to work or passage zones.
- Enhancing industrial risk management by providing a dedicated containment area to collect accidental leaks, enabling rapid and efficient interventions, and facilitating the cleaning and recovery of solvents in the event of spills.
One of our clients had an outdoor storage facility for highly flammable and/or explosive solvents, constructed several decades ago. Over time, the lack of a designated manager for the entire facility led to its gradual degradation. Inspections had been carried out partially but lacked a comprehensive overview. Several sections showed signs of insufficient maintenance, potentially leading to irreversible damage.
02. POMEX’s Role
In this context, POMEX was called upon to support the client in improving the upkeep and weekly management of outdoor industrial retention systems.
This involved :
- Completing the designation of storage zones
- Highlighting the regulatory obligations related to retention systems
- Validating the compatibility of materials with the stored solvents
- Ensuring the impermeability of structures
- Checking anti-overflow devices, leak detectors, and drainage systems
- Monitoring sufficient cleaning of installations to allow periodic inspections
- Refining inspection and patrol procedures for the facilities
- Precisely identifying responsible parties and clarifying their interactions
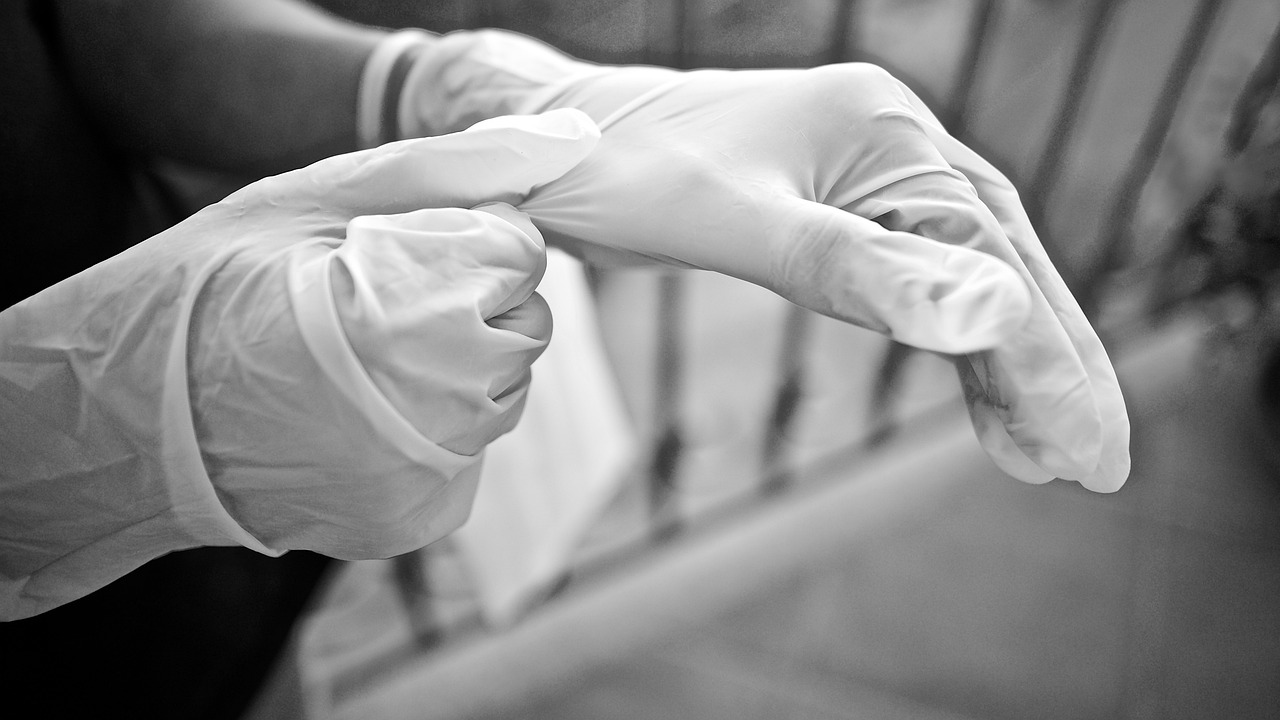
03. Implemented Solutions
After verifying the compatibility of hazardous solvents or chemicals confined in the same retention system and confirming retention capacities, we updated the facility layout plans and relevant retention system reference documents. This was followed by a preparatory audit that highlighted existing degradation in the retention systems and assigned each issue a relative score. This scoring system enabled us to prioritise the interventions required.
A coating was then applied to ensure the installations were watertight and to reduce the risk of deterioration caused by the stored substances. Practical solutions for draining contaminated and uncontaminated retention systems were added, simplifying the management of outdoor retention areas.
04. Achieved Results
Thanks to our intervention, the Directorate for Chemical Risk Control (DCRC) and the Major Accident Risk Unit (RAM Unit) noted significant improvements in the management of retention systems and a reduced risk of leaks that could harm the environment. The improved condition of the storage facility, with cleaner and better-maintained installations, also fostered greater staff engagement in maintaining these systems over time.
05. Long-Term Benefits
Once the retention systems were accurately mapped, identified, and upgraded, a daily management procedure involving key personnel and designated responsible parties was established. This ensures that the infrastructure can remain in compliance and enjoy an extended lifespan in proper working condition.
06. Adaptability
Any industry using hazardous solvents or liquid products must implement retention solutions that address the risks of leaks and demonstrate their integrity over time. POMEX is equipped to offer its expertise on this topic.
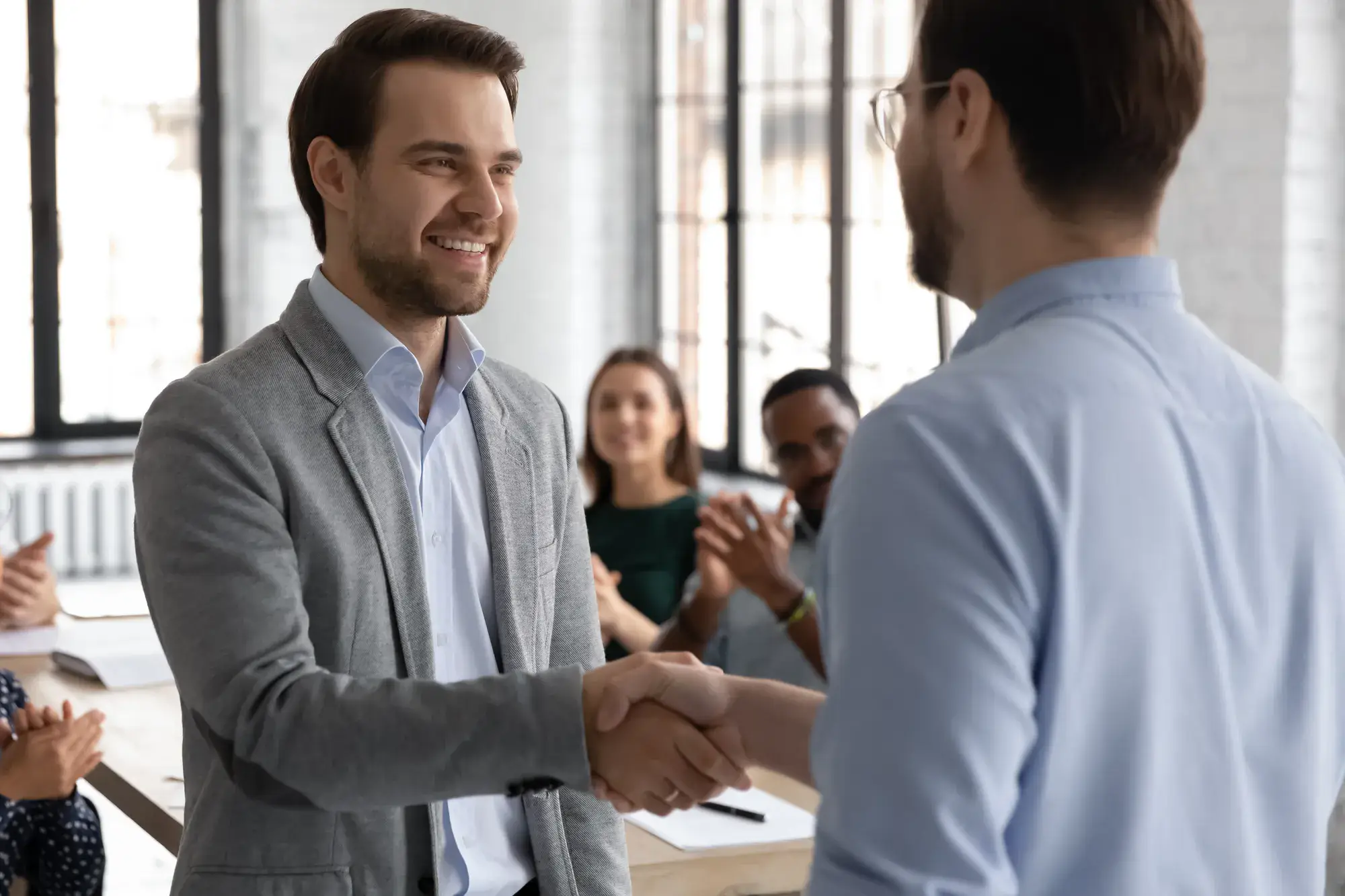
Conclusion
In summary, retention systems are a critical measure for industrial risk management and environmental protection. Their design and management must comply with strict standards to minimise the impact of accidents involving hazardous solvents.
POMEX has demonstrated that regular monitoring of these installations ensures their integrity and makes it easier to respond to potential leak scenarios by providing this collective safety barrier.