Shutdown Optimisation
L’un de nos clients a fait appel à l’expertise de POMEX pour repenser sa stratégie de maintenance.
Comment maximiser la production en optimisant la gestion des arrêts techniques ?
Découvrez comment nous avons réduit l’impact des arrêts sur la production, faisant passer la maintenance d’un simple centre de coûts à un véritable centre de profit.
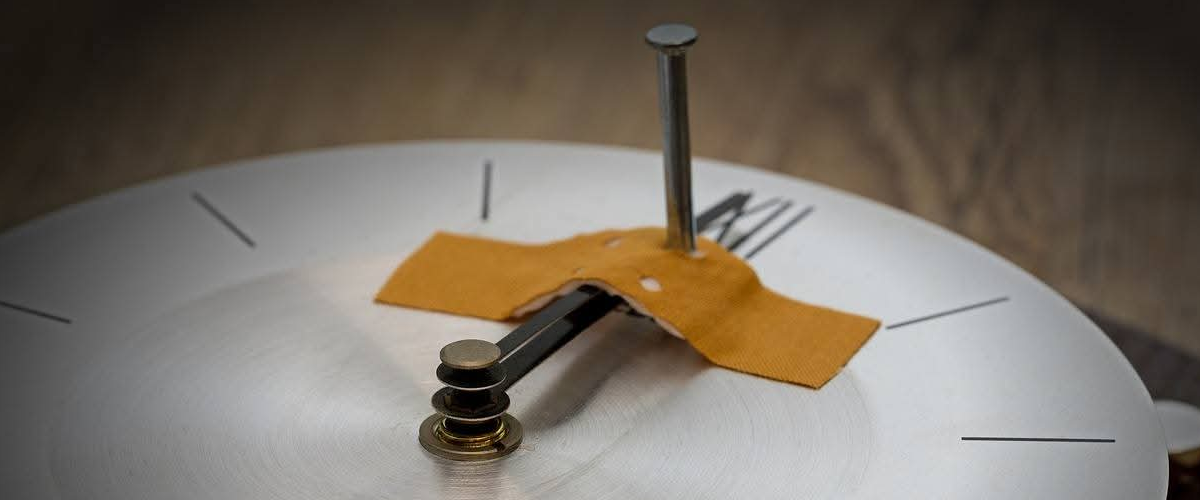
01. Contexte et problématique
L’entreprise planifiait deux arrêts techniques de deux semaines chaque année pour réaliser la maintenance de ses installations. Ces arrêts provoquaient des périodes prolongées de ramp-down (réduction des volumes de production) et de ramp-up (redémarrage progressif).
Le manque à gagner se chiffrait en millions d’euros, mais la maintenance restait cruciale pour garantir la fiabilité des équipements.
Le défi : Réduire l’impact économique de ces arrêts tout en préservant la fiabilité des infrastructures.
02. Rôle de POMEX
POMEX a collaboré avec les équipes internes pour optimiser la planification et l’exécution des arrêts techniques.
- Diagnostic initial : Évaluation des pratiques en place et identification d’opportunités de gains.
- Coordinateur “Shutdown” : Mise en place d’un poste clé pour orchestrer les arrêts plusieurs mois à l’avance. Cette personne s’appuie sur des plannings standardisés et un guide de bonnes pratiques pour préparer, exécuter et relancer efficacement la production.
- Parties prenantes : Production, maintenance, EHS, qualité, syndicats et direction.
- Méthodologie : Utilisation de la démarche DMAIC (Define, Measure, Analyze, Improve, Control) pour structurer le projet et contrôler les résultats.
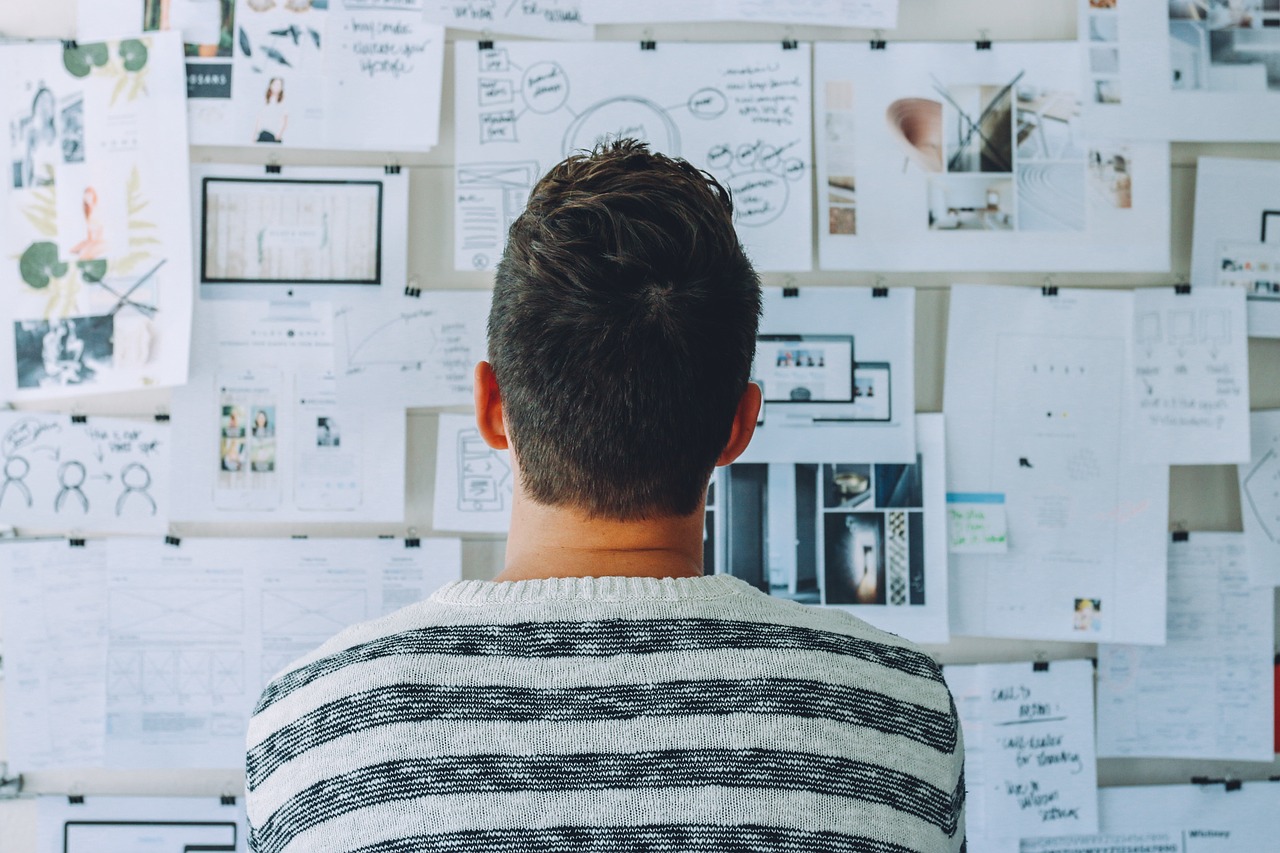
03. Solutions implémentées
Nous avons proposé de fusionner les deux arrêts annuels de deux semaines en un seul arrêt de quatre semaines. Cette approche a permis de limiter la durée globale des phases de ramp-down et ramp-up, réduisant significativement l’impact sur la production.
- Rétroplanning : Conception d’un planning standardisé pour chaque étape — préparation, exécution et remise en service des équipements.
- Optimisation des phases : Mise hors service et redémarrage de certaines zones de manière séquentielle, afin de répartir au mieux la charge de travail et d’éviter les goulots d’étranglement.
- Levée des contraintes : Adaptation des interventions en fonction des saisons (entretien des chaudières et systèmes de refroidissement), garantissant une maintenance plus fluide.
04. Les résultats obtenus ?
Les effets de ces mesures ont été immédiats et substantiels :
- Augmentation de la production : Économies de plusieurs millions d’euros grâce à la réduction des périodes d’arrêt.
- Maintien de la fiabilité : Les équipements critiques ont bénéficié d’une période dédiée à la maintenance, sans compromis sur la qualité ni perte de production.
- Amélioration des redémarrages : Standardisation des processus permettant une reprise plus rapide et plus sûre.
05. Les bénéfices à long terme
Au-delà du succès initial, POMEX a mis en place des leviers d’amélioration continue :
- Référent “Shutdown” : Un responsable dédié veille à la bonne préparation et à l’exécution optimale des futurs arrêts.
- After Action Review (AAR) : Des retours d’expérience systématiques pour affiner les pratiques après chaque arrêt technique.
- Extension du modèle : Coordination des arrêts par bâtiments, répartie sur l’année pour une meilleure gestion des ressources.
06. L’adaptabilité
La méthodologie développée peut facilement être transposée à d’autres secteurs :
- Secteurs divers : Partout où des périodes de ramp-down et de ramp-up sont nécessaires.
- Gestion du changement : Approche centrée sur l’humain pour surmonter les résistances et encourager l’adhésion.
- Outils standardisés : Le DMAIC garantit une démarche rigoureuse et reproductible dans tout environnement industriel.
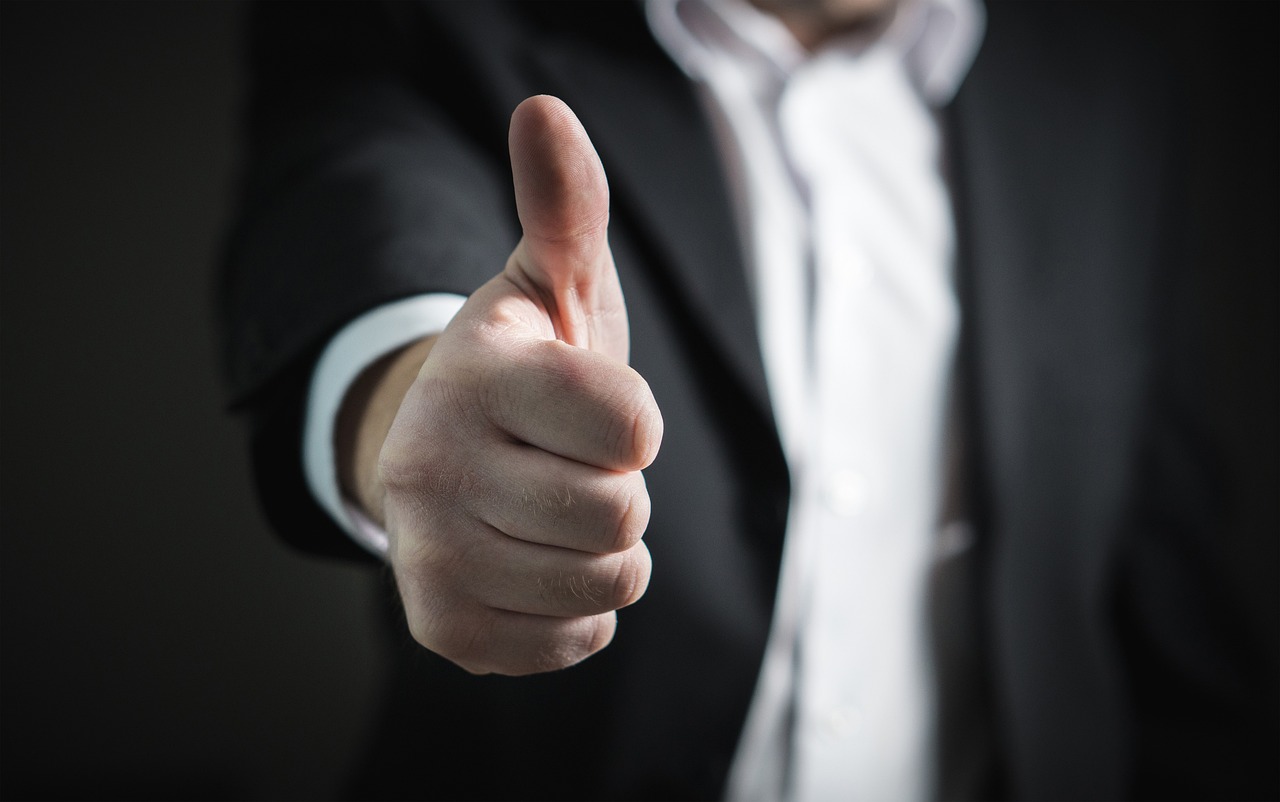
Conclusion
En repensant la gestion des arrêts techniques, POMEX a considérablement réduit les coûts liés à l’immobilisation des installations, tout en renforçant la fiabilité et l’efficacité du parc d’équipements.
Cette réussite montre qu’une approche structurée et humaine peut à la fois préserver la continuité de la production et amplifier la performance financière d’une entreprise.