Enhancing Maintenance Management
POMEX’s intervention in a a Global Pharmaceutical Leader
In the demanding environment of the pharmaceutical industry, operational performance directly depends on the ability to anticipate and swiftly resolve maintenance issues..
To address these challenges, our client enlisted the expertise of POMEX to rethink and optimise their performance indicators (KPIs). Our mission: transform maintenance KPI management to provide real-time visibility, anticipate failures, and ensure continuous operational improvement.
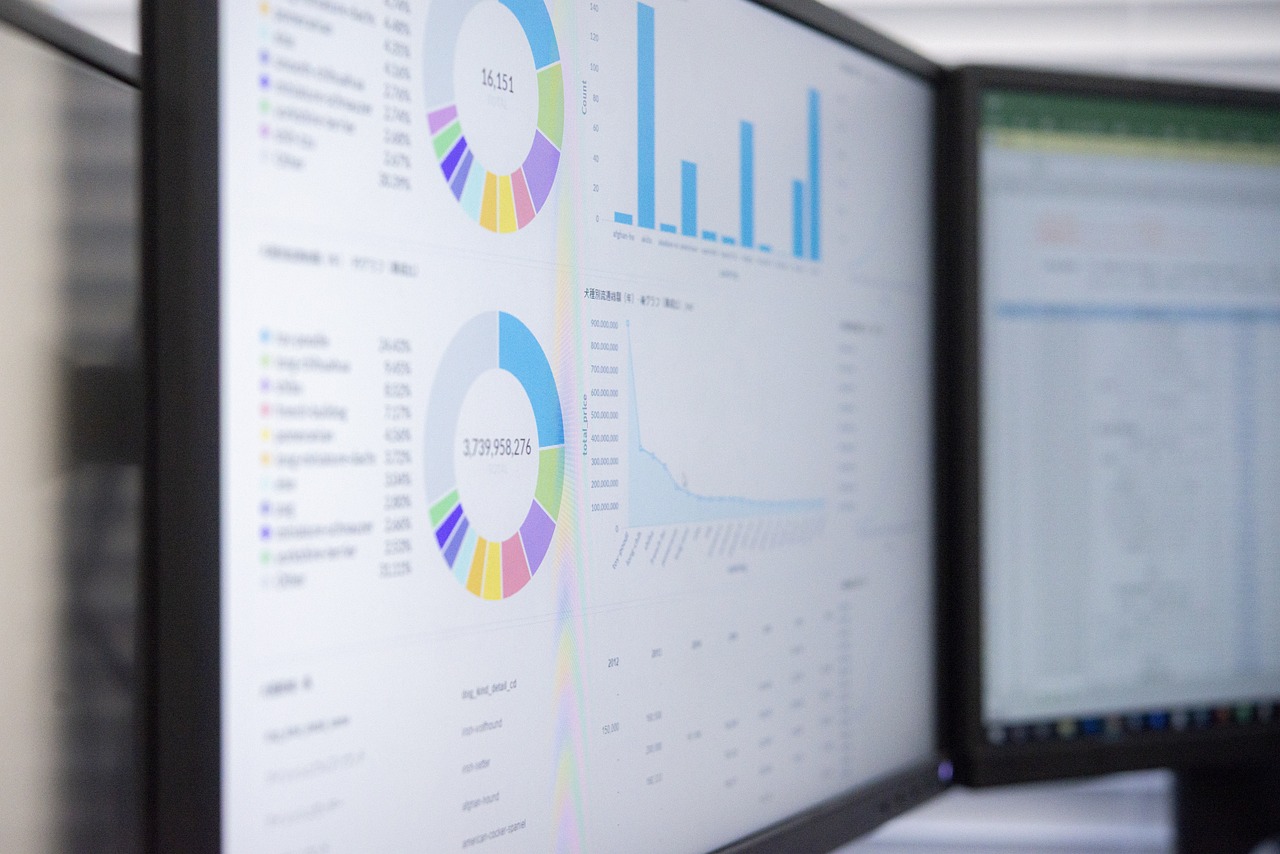
01. Context and Challenge
The client relied on a manual system to generate KPIs, focused on limited metrics such as adherence to scheduling and the proportion of completed work orders. This process, laborious and time-consuming, lacked precision and failed to offer clear visibility into future performance or evaluate the impact of corrective actions taken. Moreover, the existing KPIs no longer met the group’s requirements, creating a disconnect between the actual needs on the ground and the indicators being tracked. It became imperative to improve the system to ensure effective operational management and a detailed analysis of results.
02. POMEX’s Role
POMEX was tasked with developing a framework of leading (proactive) and lagging (retrospective) indicators to provide a comprehensive view of performance.
Our intervention focused on the following actions:
- Leading regular governance sessions to adjust actions based on leading KPIs and assess the impact of corrective measures through lagging KPIs.
- Translating the group’s new requirements into relevant KPIs.
- Collaborating closely with maintenance teams to identify critical areas for monitoring.
- Developing an automated tool in Excel, linked to SAP, to generate KPIs quickly and reliably.
- Implementing intuitive KPI visualisations for optimal use during follow-up meetings.
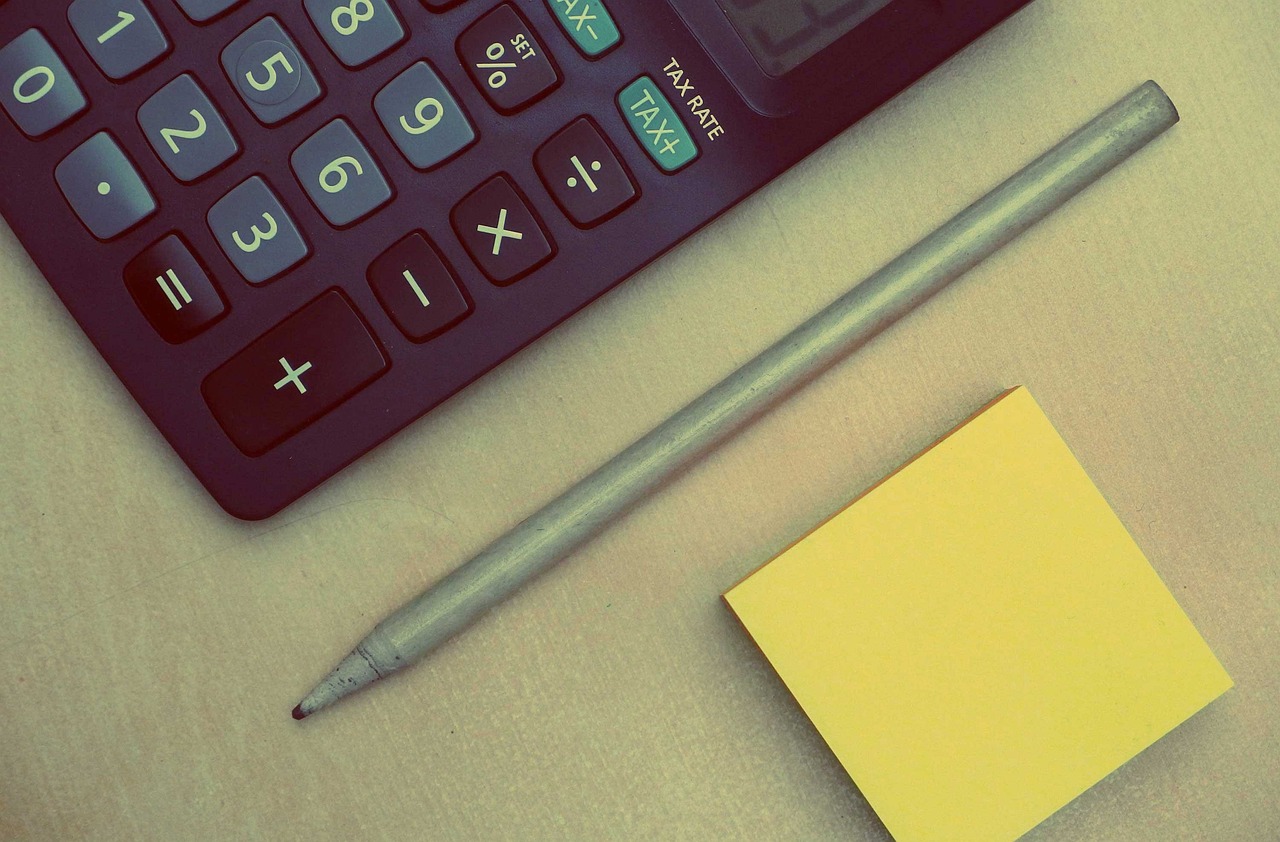
03. Implemented Solutions
We implemented an automated KPI generation system that enabled:
- Establishing a governance framework based on these indicators, enabling proactive monitoring and swift adjustments in case of performance deviations.
- Complete automation of KPI generation, reducing the need for manual processing.
- A clear distinction between leading KPIs (to anticipate issues and proactively manage) and lagging KPIs (to validate the effectiveness of actions taken).
04. Achieved Results
The solutions implemented by POMEX yielded concrete, measurable results:
- Team satisfaction: The new tool was quickly adopted by the maintenance teams, who appreciated its ability to provide a comprehensive, real-time view of performance.
- Reduction in KPI generation time: The production time for indicators decreased from several hours to just minutes, freeing teams to focus on higher value-added tasks.
- Better problem anticipation: Thanks to the leading KPIs, risks were identified earlier, allowing proactive implementation of corrective measures.
- Improved performance: The lagging KPIs confirmed the positive impact of corrective actions, with key indicators turning green after the solutions were deployed.
05. Long-Term Benefits
The integration of leading and lagging KPIs enabled proactive and continuous performance management. The leading indicators help prevent problems before they become critical, while the lagging indicators provide a reliable check on the impact of actions. This framework ensures continuous operational improvement and strategic performance tracking, securing long-term results.
06. Adaptability
The KPI management model developed by POMEX is adaptable to other sectors. As a universal framework, it enables proactive management and accurate measurement of results in any field requiring operational performance optimisation. Its effectiveness has already been demonstrated in various industrial contexts.
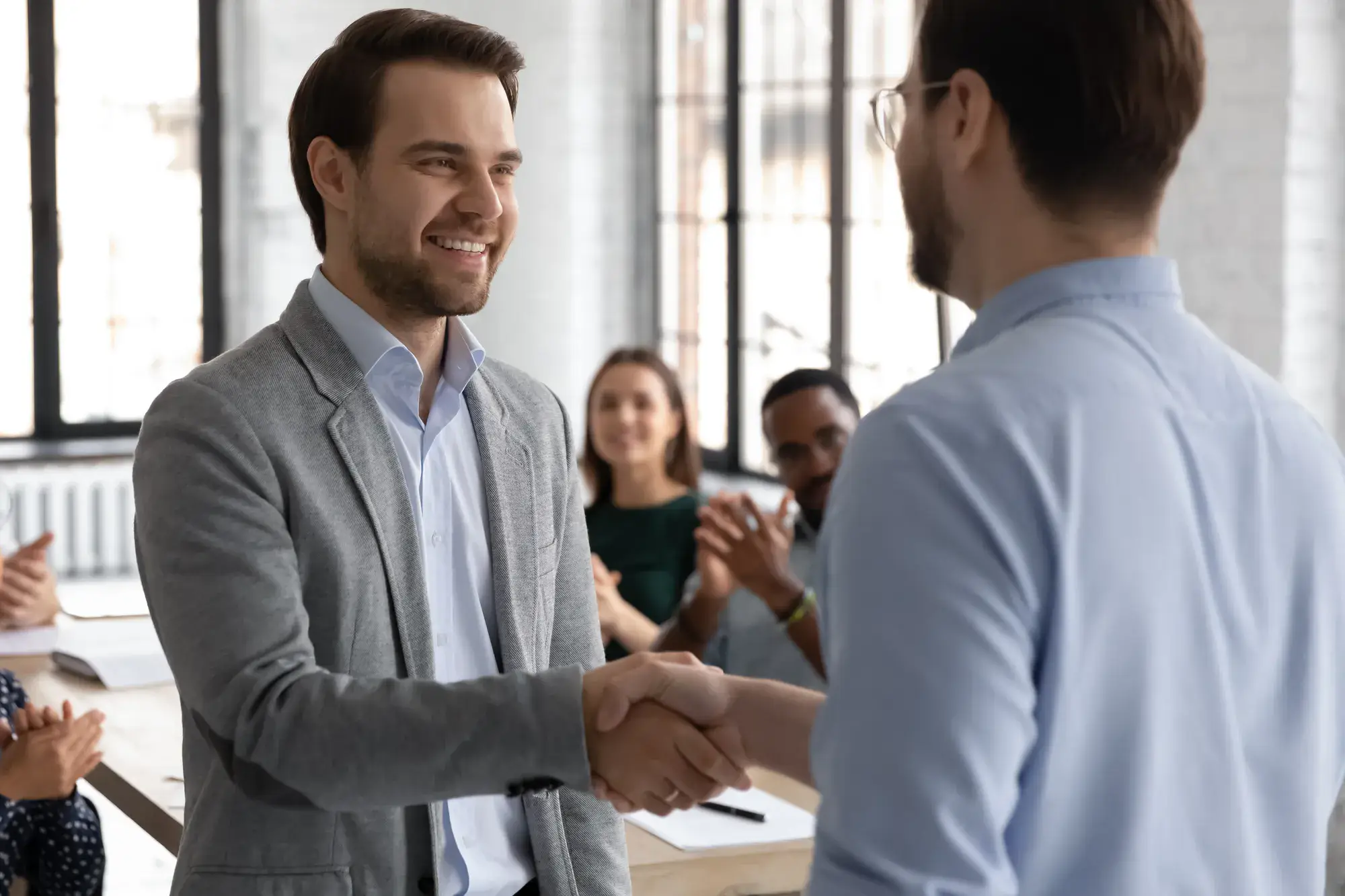
Conclusion
By transforming the client’s KPI management, POMEX not only optimised the generation of indicators but also established proactive management and problem anticipation. Through an approach based on leading and lagging KPIs, we ensured continuous operational improvement and sustainable maintenance performance management.