How to turn a regulatory constraint into an opportunity for operational excellence ?
POMEX and the SEVESO Directive
A solvent storage facility, composed of outdated installations, needed to comply with the latest SEVESO regulatory requirements.
Here’s how POMEX successfully turned this situation into a remarkable opportunity.
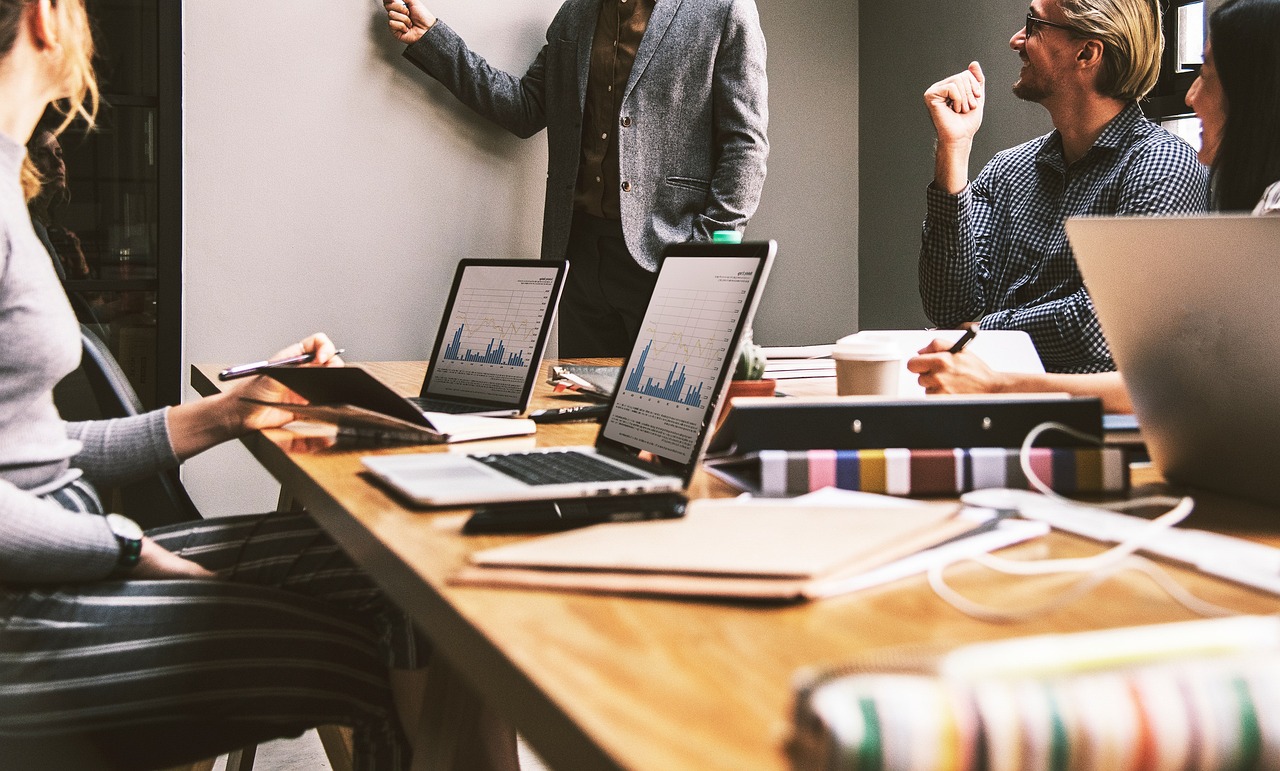
01. Context and Challenge
The storage facility, designed for highly flammable and/or explosive solvents, underwent a regulatory audit. This audit uncovered several major and minor non-conformities with the strict requirements of the SEVESO directive.
These gaps primarily concerned:
- Installation safety
- Industrial risk management
- Compliance of equipment with current standards
The facility urgently needed to address these non-conformities to ensure operational continuity without compromising the safety of staff, the environment, or nearby installations. Developing an effective action plan to respond to the audit’s findings became imperative.
02. POMEX’s Role
It was in this context that POMEX was called upon to provide its expertise. Our mission was to assist the client in drafting, implementing, monitoring, and executing an action plan to meet the requirements of the SEVESO directive.
In close collaboration with technical teams (engineering and maintenance), HSE managers, and the site management, POMEX played a key role in optimising the installations to ensure risk control and safety.
To achieve this, it was crucial to:
- Understand the operations of the storage facility and its stakeholders.
- Account for inspection and logistical constraints to define intervention priorities.
A thorough analysis of the existing infrastructure enabled us to develop a comprehensive and specific action plan.

03. Implemented Solutions
Our intervention was structured into several project phases, each tailored to the client’s initial priorities and adjusted based on findings from the preceding phase.
We implemented the following:
- Corrective actions on critical equipment
- Improved industrial risk management procedures
- Enhanced and reinforced safety measures to prevent major accidents
- New procedures were formalised, including control protocols and updated templates highlighting the preparatory and execution stages for periodic and safety inspections.
- New technical standards were integrated and applied across all installations, reducing risks associated with storing flammable and explosive solvents.
Each solution was rigorously evaluated for feasibility and site impact. Close collaboration with each affected department ensured that necessary actions were planned and executed with minimal operational disruption. Communication with internal teams and External Technical Control Services (ETCS) was vital to the project’s success, ensuring adoption of new practices and understanding of the objectives.
04. Achieved Results
Thanks to our intervention, the storage facility successfully addressed all major non-conformities within the deadlines imposed by the Directorate for Chemical Risk Control (DCRC) and the Major Accident Risk Unit (RAM Unit), which oversees SEVESO-classified companies. This ensured the safe continuation of operations.
Beyond this immediate success, our mission also resulted in a complete overhaul of the periodic inspection programme for managing process and storage equipment. The new system is more robust, and the staff no longer view regulatory constraints as a burden but rather as an opportunity to improve both safety and the facility’s operational efficiency.
05. Long-Term Benefits
The best practices we implemented not only resolved immediate issues but also laid the groundwork for continuous improvement. The facility now has formalised processes for risk management, supported by trained and safety-conscious personnel.
A full transfer of expertise took place between POMEX’s specialists and the internal teams, ensuring the long-term sustainability of the solutions provided. The client is now capable of maintaining safety and compliance standards over time while continuing to refine their practices.
06. Adaptability
The methodology we deployed can be adapted to a wide range of industrial sites subject to strict regulations, such as the SEVESO directive or other industrial risk management standards. Analysing processes, identifying non-conformities, and implementing tailored action plans are approaches that POMEX masters and adjusts to meet the specific needs of each client.
This approach has already proven effective in other industrial compliance projects, demonstrating its flexibility and reliability.
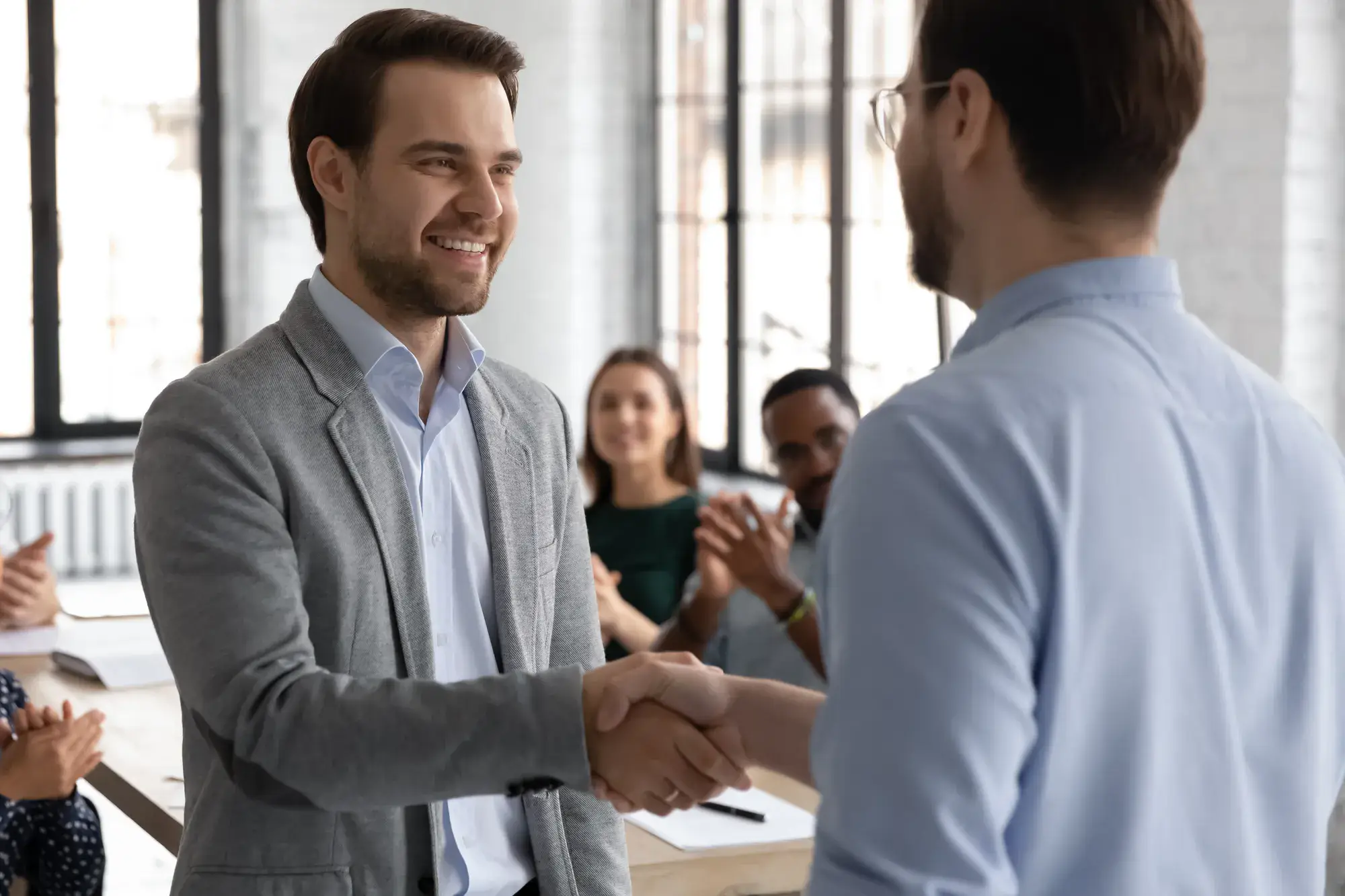
Conclusion
This experience demonstrated that managing non-conformities and industrial risks can be transformed into a true opportunity. By involving all departments and teams in the change process, we successfully addressed the facility’s non-conformities while sustainably improving safety and risk awareness within the company.
POMEX has shown that, through a rigorous and collaborative approach, it is possible to turn a regulatory challenge into an opportunity for long-term improvement. We are proud to have contributed to this success and are ready to assist other companies in their compliance and industrial risk management efforts.