Shutdown Optimisation
One of our clients turned to POMEX’s expertise to rethink their maintenance strategy.
How can production be maximised by optimising the management of technical shutdowns ?
Discover how we minimised the impact of shutdowns on production, transforming maintenance from a simple cost centre into a genuine profit centre.
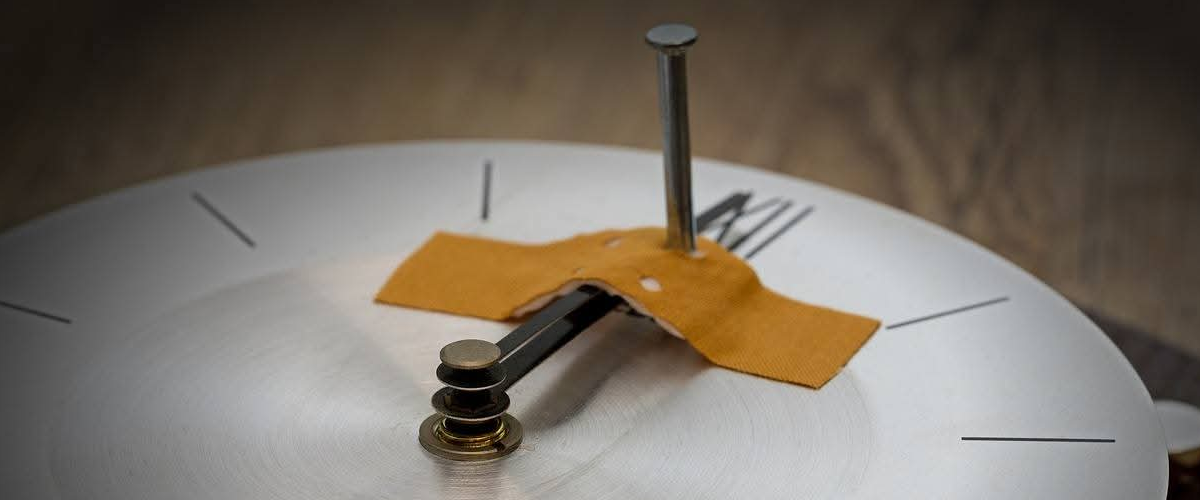
01. Context and Challenge
The company scheduled two two-week technical shutdowns each year to carry out maintenance on its facilities. These shutdowns resulted in prolonged ramp-down (reduction in production volumes) and ramp-up (gradual restart) periods. The resulting financial losses amounted to millions of euros, yet maintenance was essential to ensure the reliability of the equipment.
The challenge : To reduce the economic impact of these shutdowns while preserving the reliability of the infrastructure.
02. POMEX’s Role
POMEX collaborated with internal teams to optimise the planning and execution of the technical shutdowns.
- Initial assessment : An evaluation of current practices to identify potential gains.
- “Shutdown Coordinator” role : Establishing a key position to orchestrate shutdowns several months in advance. This role relied on standardised schedules and a best practices guide to prepare, execute, and restart production effectively.
- Involving stakeholders : Including production, maintenance, EHS (Environment, Health, and Safety), quality, unions, and management.
- Methodology : Using the DMAIC approach (Define, Measure, Analyse, Improve, Control) to structure the project and monitor results.
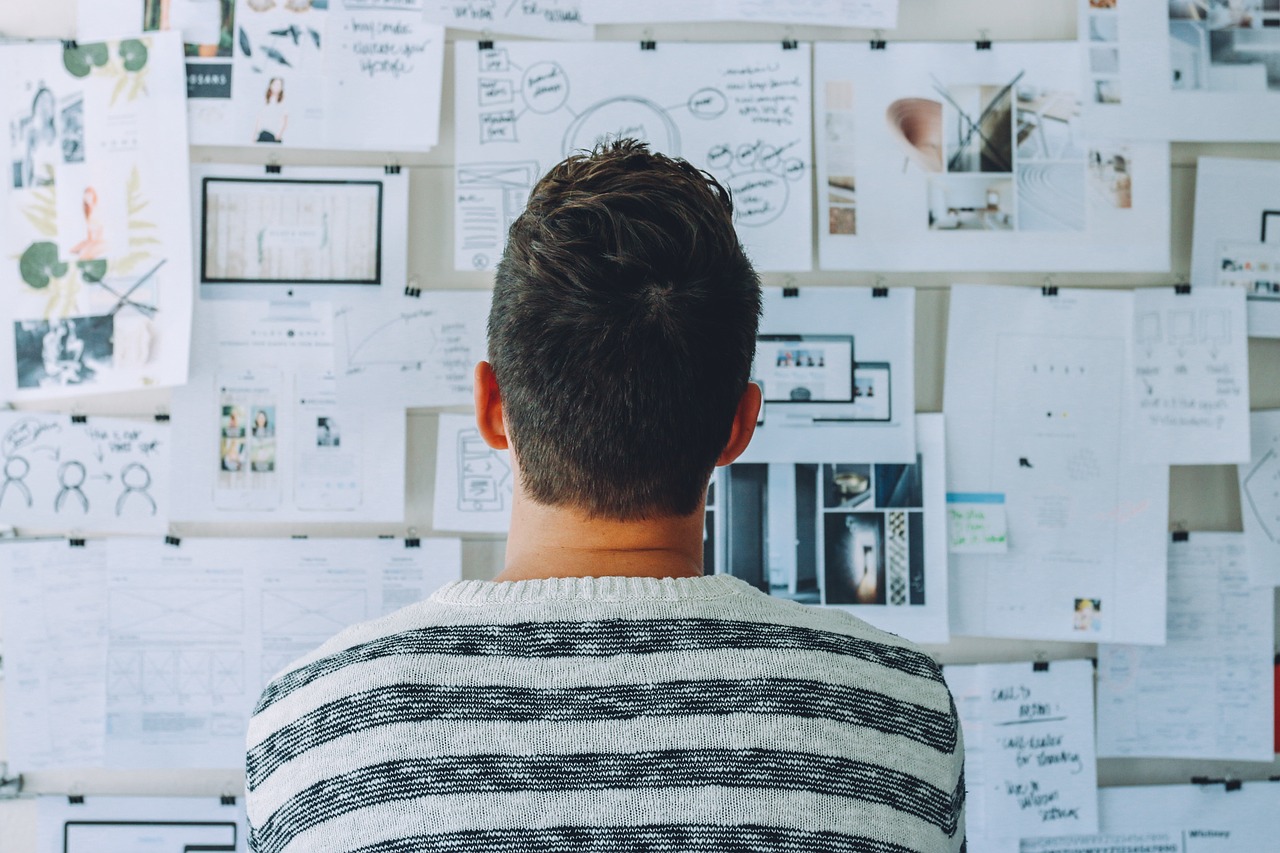
03. Implemented Solutions
We proposed merging the two annual two-week shutdowns into a single four-week shutdown. This approach reduced the overall duration of ramp-down and ramp-up phases, significantly limiting the impact on production.
- Backwards planning : Creating a standardised timeline for each stage – preparation, execution, and recommissioning of equipment.
- Phase optimisation : Sequentially shutting down and restarting specific zones to better distribute the workload and avoid bottlenecks.
- Eliminating constraints : Adapting maintenance tasks to seasonal conditions (e.g., servicing boilers and cooling systems) to ensure smoother operations.
04. Achieved Results
The impact of these measures was immediate and substantial:
- Increased production : Savings of several million euros due to shorter shutdown periods.
- Preserved reliability : Critical equipment received a dedicated maintenance period, ensuring quality without compromising production.
- Improved restarts : Standardised processes enabled faster and safer production resumption.
05. Long-Term Benefits
Beyond the initial success, POMEX introduced measures to ensure continuous improvement:
- Dedicated “Shutdown Coordinator” : A dedicated manager oversees the preparation and optimal execution of future shutdowns.
- After Action Review (AAR) : Systematic feedback sessions to refine practices after each technical shutdown.
- Scaling the model : Shutdowns were coordinated by building and staggered throughout the year to optimise resource management.
06. Adaptability
The developed methodology is easily transferable to other sectors:
- Diverse industries : Applicable wherever ramp-down and ramp-up periods are necessary.
- Change management : A people-centred approach to overcome resistance and encourage engagement.
- Standardised tools : The DMAIC framework ensures a rigorous and reproducible process across all industrial environments.
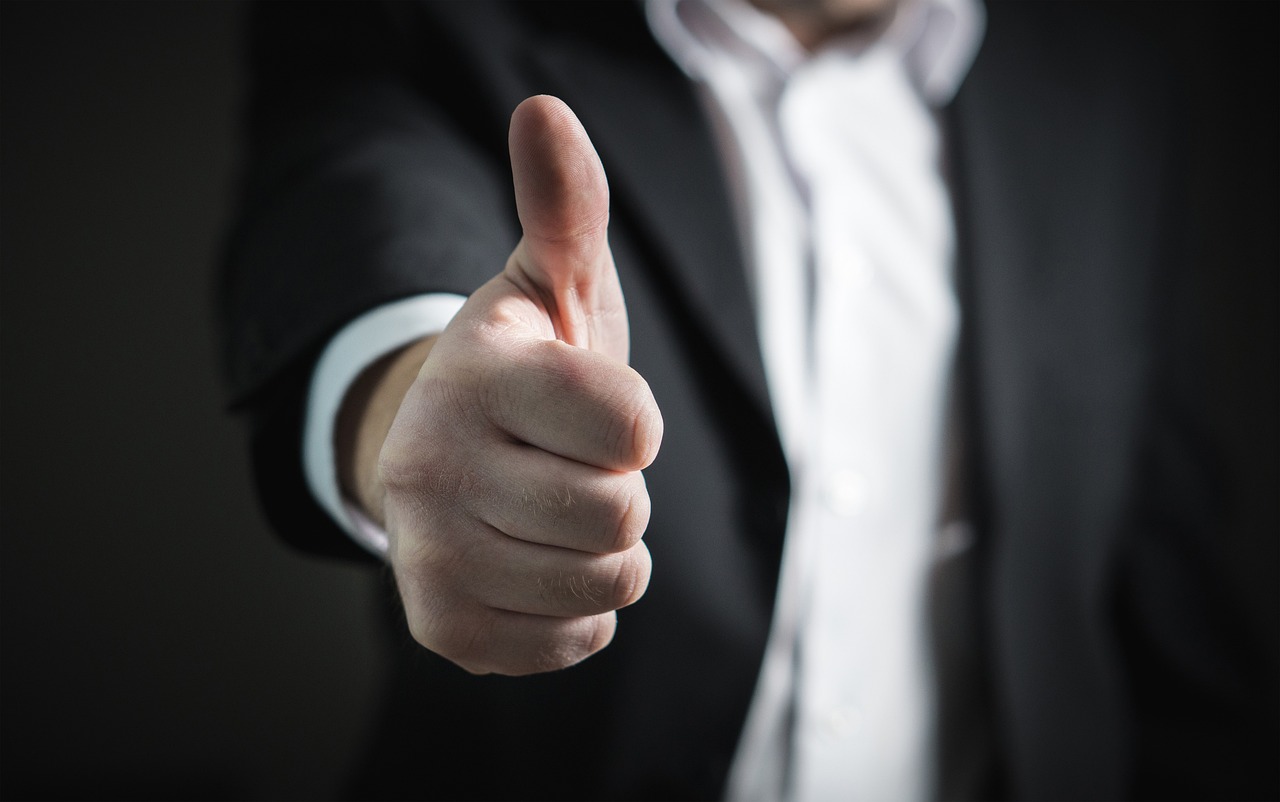
Conclusion
By rethinking the management of technical shutdowns, POMEX significantly reduced the costs associated with downtime while enhancing the reliability and efficiency of the equipment.
This success demonstrates that a structured, human-centred approach can not only maintain production continuity but also boost the financial performance of a business.