The art of optimising format changes
POMEX’s intervention on a production line
Here is how POMEX contributed to reducing downtime and increasing productivity during format changes.
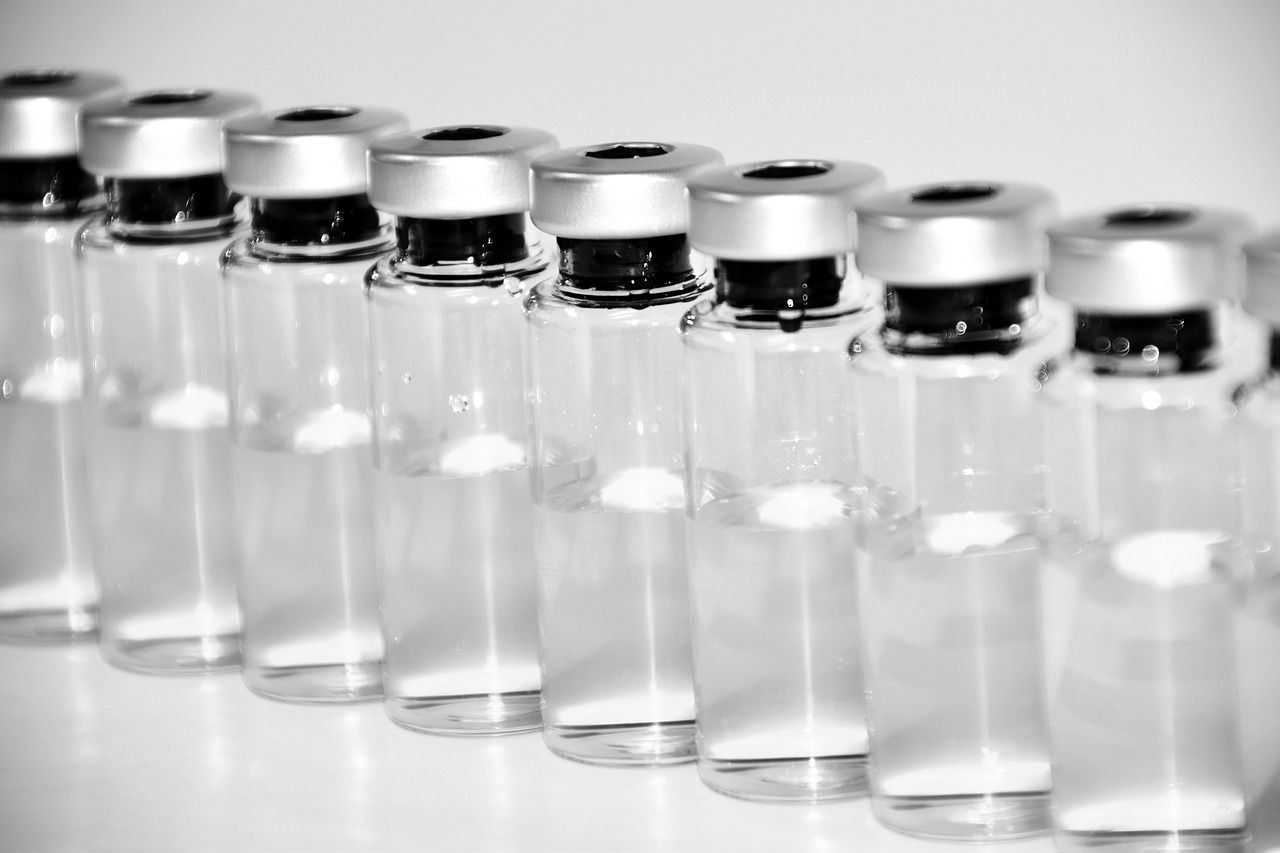
01. Context and Challenge
The client company, a leader in high-speed production, was facing critical issues related to format changes on one of its production lines.
These operations consumed hours, immobilising the line and leading to several negative consequences :
- Inoperable line : No production could occur during the format change.
- Team demobilisation : A portion of the staff was underutilised.
- Technical frustration : Inaccurate adjustments during restart caused stress and errors.
These issues directly threatened the company’s output and the motivation of its teams. The client sought to drastically reduce downtime while avoiding adjustment problems during restarts.
02. POMEX’s Role
Our mission was to carry out a SMED (Single Minute Exchange of Die) project to reduce the duration of format changes. To achieve this, we involved various stakeholders: the management hierarchy, production operators and technicians, the Operational Excellence team, and the equipment and spare parts supplier.
Using the SMED method, the objectives were to :
- Segment operations : Identify complete subassemblies to replace, converting hours of disassembly into minutes of swapping parts.
- Optimise logistics : Use prepared trolleys containing replacement parts, enabling changes during hidden time.
- Prevent errors : Implement error-proofing devices to minimise incorrect assembly.
- Standardise processes : Create clear procedures to ensure a quick and smooth restart.
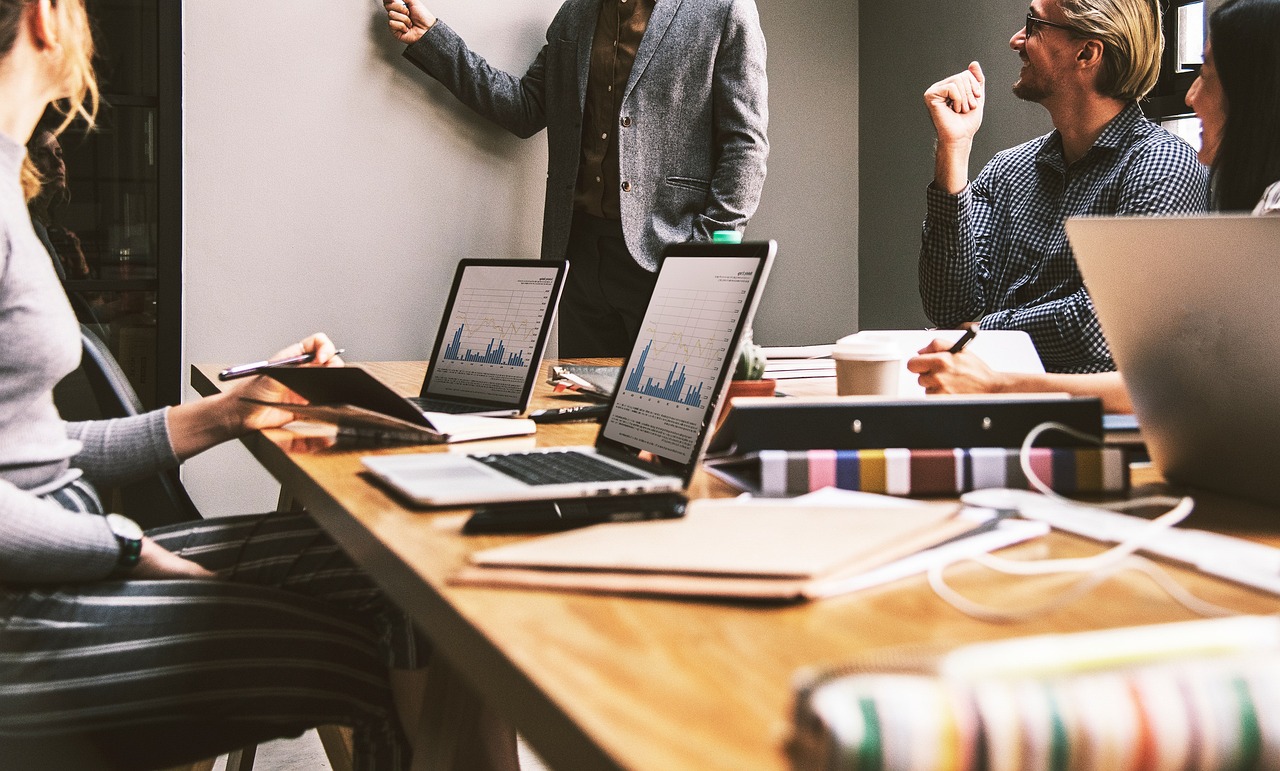
03. Implemented Solutions
We implemented the following measures :
- Preparation of SMED kits : Preassembled and preadjusted parts.
- Reconfiguration of steps : Testing, document analysis, and collaboration with suppliers to ensure compatibility.
- Documentation and training : Formalising procedures and raising team awareness.
04. Achieved Results
The solutions implemented by POMEX delivered concrete results :
- Significant improvement in OEE (Overall Equipment Effectiveness) : Format change times were reduced from several hours to just a few minutes.
- Increased team satisfaction : Elimination of inaccurate adjustments and associated frustrations.
- Secondary benefits : Increased machine reliability and systematic revision of replaced components.
These results were very well received by stakeholders, strengthening confidence and internal motivation.
05. Long-Term Benefits
Our client applied these improvements to other production lines. As a bonus, they continued to monitor format change times to prevent any backsliding.
06. Adaptability
A similar model has been used to minimise machine downtime for repairs by employing ready-to-use kits. A further example of efficiency comes from the inspiration of Formula 1 pit stops.
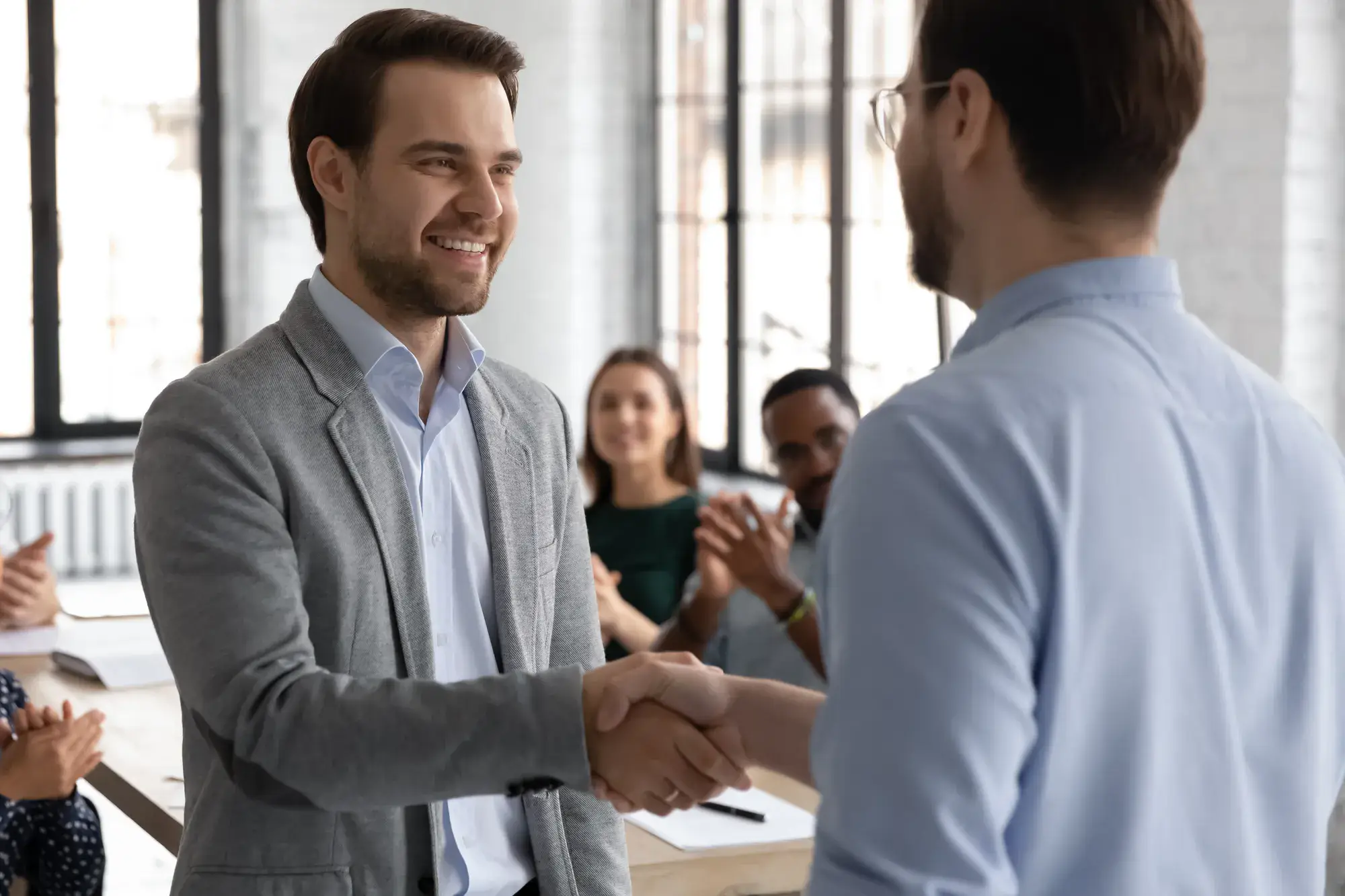
Conclusion
This project highlighted the importance of a structured and collaborative approach to resolving complex issues. It is vital to step back, analyse each operation, and involve all stakeholders.
A final tip : Film your operations to study them objectively. Involve all relevant teams to ensure an effective and well-accepted solution.